TSW R&D Study: Embodied Carbon Content of Common Building Materials
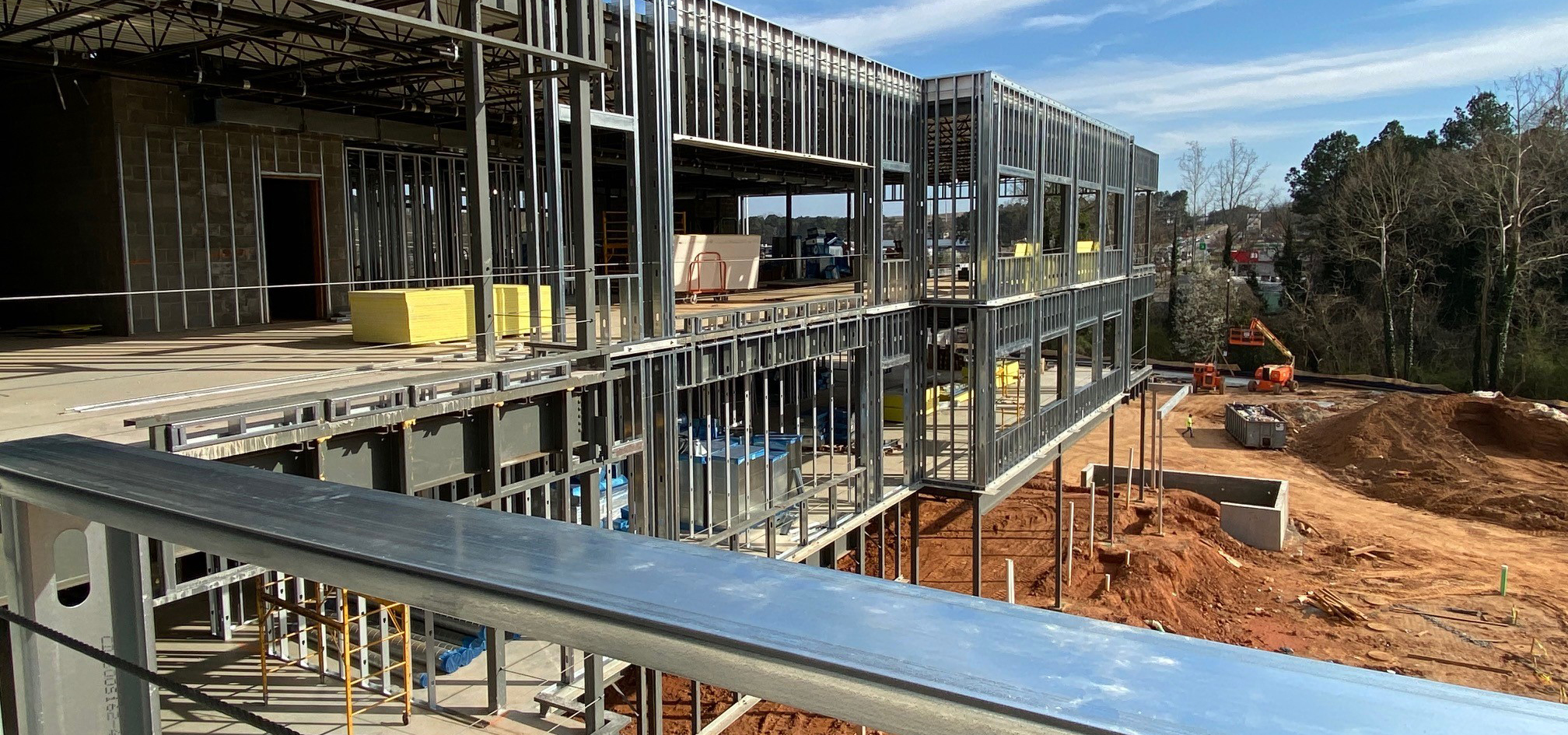
Prepared by Alex Fite-Wassilak and Chris Morphis
TSW R&D Study: Embodied Carbon Content of Common Building Materials – As designers of buildings and landscapes, we understand that construction can lead to emissions of greenhouse gases and other environmental impacts. In fact, materials used for construction make up about 11% of global carbon emissions annually. With the United Nations identifying the next 20 years as crucial for avoiding worst-case climate change scenarios, we have begun researching the embodied carbon content of common construction materials. This includes the “lifecycle carbon” – the sum of CO2 emissions from manufacturing, transportation, installation, maintenance, and disposal – and “Embodied Carbon” – emissions from initial sourcing and manufacturing of materials. By understanding the relative amounts of embodied carbon in materials, we can make informed design decisions and choose lower-carbon materials, moving towards carbon neutrality or net-positive emissions. In our initial research, we are focusing on “cradle-to-gate” embodied carbon, which includes manufacturing but excludes transportation, installation, maintenance, and disposal. This phase is the largest contributor of emissions in the material lifecycle, and the easiest to calculate. We report all calculations in kilograms of CO2-equivalent (kgCO2eq) and materials are reported in increments of cubic meters (or square meters for insulation) for accurate comparison of global warming potentials. Comparisons of common building materials are documented in the table below:
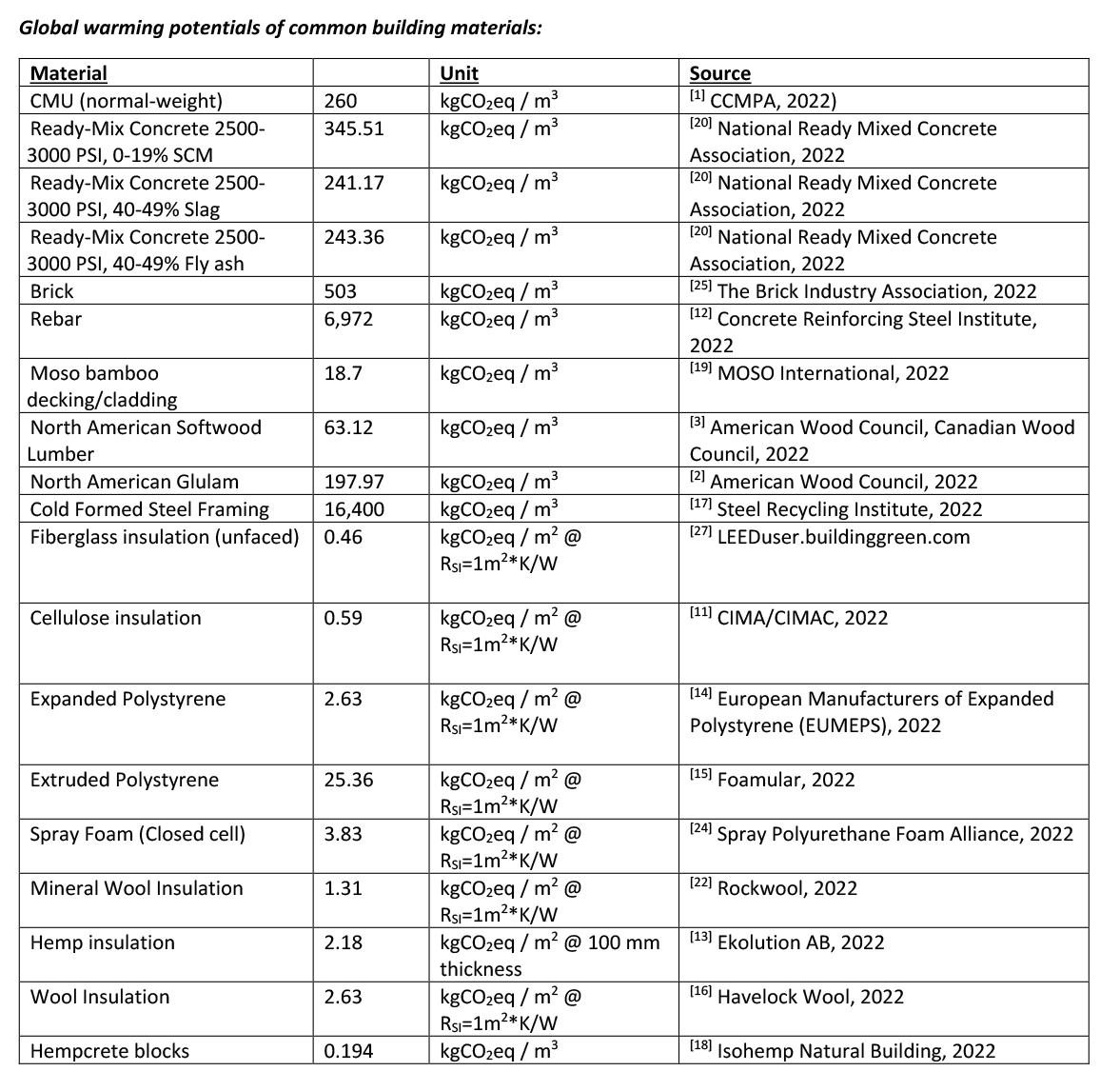
A couple broadly applicable rules of thumb for reducing embodied carbon in construction projects are that renovating an existing building is the most carbon efficient option, and materials with recycled content are more carbon efficient than virgin materials. [10] In general, most projects can feasibly achieve a 20% reduction in embodied carbon via strategic substitution of commonly available materials. Greater reduction of around 60% can be accomplished by increasing the use of already available but uncommonly-used low-carbon materials. An even more thorough transition to carbon-positive design can be achieved by the development and adoption of biogenic and mineral materials that are now in various stages of research and development, along with more comprehensive design changes that go beyond material substitutions and encompass architectural form and the advancement of novel supply chains. [10] Notably on this matter, recent research has found that at the municipal scale a high-density low-rise development pattern yields the lowest long-term emissions. This is contrary to the conventional understanding that the highest possible density is the most energy efficient. The study found that very tall buildings have much higher lifecycle energy requirements than low- and mid-rise development. The implication of this finding is that walkable, human-scale places like Paris, Washington DC, or Las Catalinas are not just great for human comfort, but also for environmental benefits.[28]
Concrete
Concrete is ubiquitous in construction, and accounts for 6-10% of CO2 emissions worldwide[7]. The most effective ways to reduce carbon emissions from concrete are, first, to limit its use, and second to modify its composition [10]. More-so than any other construction material, concrete has a flexible composition that allows for variation of the mixture used to make it. The formula can be modified to reduce the embodied carbon content. The technical aspects of doing so are complex, but there are a couple of general principles. Concrete is made from cement, aggregate, water, and air. Because cement is the highest-carbon ingredient of concrete, the embodied carbon level can be modified by adjusting the mix to reduce the quantity of cement and replace it with more aggregate (of a specific type, known as “supplementary cementitious materials”). Data from the National Ready Mixed Concrete Association indicates that boosting the slag or fly ash content of concrete from a conventional 20 percent level to 50 percent results in a 30 percent reduction in carbon [20]. Additional considerations to minimize carbon and ensure quality are to allow for a 56 or 90-day cure time rather than the standard 28 days [10], to source SCM aggregates locally, and to use type IL cement (Portland Limestone Cement) instead of conventional Portland Cement [7].
Steel
The carbon footprint of steel can vary dramatically depending on the method by which it is manufactured. In general, the best way to minimize embodied carbon in steel is to use recycled material. Steel that has been recycled has 5x less carbon than virgin steel on average. The simplest way to source recycled steel is to purchase it from a facility that uses electric arc furnaces (EAC) instead of Basic Oxygen Furnaces (BOF). EAC’s are generally only capable of processing recycled steel and emit substantially less carbon [8]. Utilizing high recycled content rebar can result in a 4%-10% reduction in carbon versus the baseline alternative. [23] Notably, though, steel has a substantially higher carbon content than any other material reviewed in this study. The most effective way to minimize the carbon footprint from steel is to use less of it.
Wood
Wood has a substantially lower embodied carbon content than steel or concrete and is a naturally regenerative material. In general, it is a preferable material alternative to both concrete and steel. However, there are still significant carbon impacts associated with its use, including forestry practices, transportation, milling, and manufacturing. The most impactful ways to minimize the carbon content of wood is to specify the use of reclaimed wood or wood that is sustainably harvested, air-dried rather than kiln-dried, and manufactured with renewable energy or otherwise energy-efficient processes. [5]
In buildings, consider substituting steel structural components with glulam engineered wood [10]. Glulam is comprised of wooden strips laminated together with adhesive; it is stronger than steel by weight[26] and contains roughly 1.2% as much embodied carbon as steel. [3] [17]
Bamboo
Bamboo is useful for pole construction, concrete reinforcement, and manufactured products such as finishes, panels, and tiles. It has a high strength-to-weight ratio and can be harvested sustainably; bamboo plants do not die when cut and regenerate rapidly. As with trees, sustainable harvesting is an important consideration. Try to source locally. Fortunately, the Southeastern United States is a bamboo-growing region. As with timber, bamboo must be dried, so be sure to specify low-carbon drying methods.[6] Carbon content varies and an industry average has not yet been established, but one variety of bamboo decking/cladding contains roughly 30% of the embodied carbon as a comparable quantity of timber. [19] [4]
Insulation
Biological- and mineral-based materials, including cellulose, hemp fiber, straw, wool, fiberglass, and mineral wool, have substantially less embodied carbon than petrochemical-based insulation materials. For example, cellulose insulation (made from recycled paper and cardboard) contains just 22% of the embodied carbon of expanded polystyrene and 2% of the embodied carbon of extruded polystyrene [11], [14], [15]. Biotic materials also have lower R-values by mass than petrochemical insulation, and thus require more volume to achieve the same insulating effect. Even so, they tend to be net carbon sequestering [23] by virtue of their their composition as renewable biotic materials and their low energy costs to produce.
Fiberglass insulation and mineral wool insulation both contain significant amounts of recycled content. Both are recyclable. Some mineral wool insulations are produced with slag, which is a waste material that would otherwise be landfilled. Fiberglass and mineral wool also have fire retardant properties, in contrast to foam and natural fiber insulations. [27][22] Both materials are widely used and have competitive embodied carbon contents compared to natural fiber insulations. Thus they are ideal insulation materials, particularly if high-recycled content products are specified.
Materials In Development
Fibers from hemp, straw, coconut, and seaweed all have the capacity for incorporation into building materials, as do compressed earth blocks and wool insulation. These are already produced in abundance as agricultural products, and many have been trialed for building applications.[10] Generally, a shift towards biologically synthesized fibers is advantageous because it utilizes renewable resources that are less energy-intensive to manufacture. Mass adoption of such materials will require further development of production standards, manufacturing processes, and supply chains. Some potential limitations to adopting these materials in development include existing building codes and durability concerns relating to moisture, humidity, and fire resistance. [10] Case studies and small-scale deployment of these materials indicates that they have great potential for high-quality architectural applications.
We hope that this article is informative for designers and clients alike when making decisions to reduce or minimize the environmental impact of a project. Another approach TSW is taking to lessen the embodied carbon of materials we design includes using carbon calculators. We recognize that there are many new developments in tools to help minimize the embodied carbon of your project. We are always excited to work with clients to help create projects that have a positive impact on the health and safety of the occupants and the broader environment.
References
[1] CCMPA (2022). Environmental Product Declaration: Normal-Weight and Light-Weight Concrete Masonry Units as Manufactured by Members of CCMPA. Retrieved from https://ccmpa.ca/wp-content/uploads/2021/01/311.EPD_for_CCMPA_Normal-Weight_And_Light-Weight_Concrete_Masonry_Units.pdf
[2] American Wood Council. (2022). Retrieved from Environmental Product Declaration: North American Glue Laminated Timbers: https://www.awc.org/pdf/greenbuilding/epd/AWC-EPD-Glulam-1307.pdf
[3] American Wood Council, Canadian Wood Council. (2022). Environmental Product Declaration: North American Softwood Lumber. Retrieved from American Wood Council: https://www.awc.org/pdf/greenbuilding/epd/AWC_EPD_NorthAmericanSoftwoodLumber_20200605.pdf
[4] architecture2030.org. (2022). Retrieved from https://architecture2030.org/why-the-building-sector/
[5] architecture2030.org. (2022). Retrieved from Carbon Smart Materials Pallette – Wood: https://materialspalette.org/wood/
[6] architecture2030.org. (2022). Retrieved from Carbon Smart Materials Palette – Bamboo: https://materialspalette.org/bamboo/
[7] architecture2030.org. (2022). Carbon Smart Materials Palette – Concrete. Retrieved from https://materialspalette.org/concrete/
[8] architecture2030.org. (2022). Carbon Smart Materials Palette – Steel. Retrieved from https://materialspalette.org/steel/
[9] ASTM International. (2022). Environmental Product Declarations. Retrieved from ASTM International: https://www.astm.org/products-services/certification/environmental-product-declarations/epd-pcr.html
[10] Carbon Leadership Forum. (2022). Carbon Storing Materials Summary Report, February 2021. Retrieved from Carbon Leadership Forum: https://carbonleadershipforum.org/carbon-storing-materials/
[11] CIMA/CIMAC. (2022). Industry-Wide Type III EPD: Conventional Loose-Fill Cellulose Insulation. Retrieved from https://www.cellulose.org/images/EPD_CIMA_CIMAC_Conventional_Loose-Fill_Cellulose_Insulation_JAN20-1.pdf
[12] Concrete Reinforcing Steel Institute. (2022). Environmental Product Declaration – Fabricated Steel Reinforcement. Retrieved from https://www.crsi.org/cfcs/cmsIT/baseComponents/fileManagerProxy.cfc?method=GetFile&fileID=83406608-EB89-B478-754D2D0CDBC4D12A
[13] Ekolution AB. (2022). Environmental Product Declaration: Ekolution Hemp Fibre Insulation. Retrieved from https://portal.environdec.com/api/api/v1/EPDLibrary/Files/b1030640-bd7d-46f0-9bce-b4ce6335b672/Data
[14] European Manufacturers of Expanded Polystyrene (EUMEPS). (2022). Environmental Product Declaration: Expanded Polystyrene (EPS) Foam Insulation. Retrieved from https://epd-online.com/PublishedEpd/Download/9572
[15] Foamular. (2022). Environmental Product Declaration: Foamular Extruded Polystyrene (XPS) Insulation. Retrieved from http://www.owenscorning.com/networkshare/EIS/10018927%20EPD%20-%20FOAMULAR%20Insulation.pdf?id=2147489289
[16] Havelock Wool. (2022). LCA Results and Interpretation: Havelock Wool Batt and Loose-fill Insulation . Retrieved from https://www.transparencycatalog.com/company/havelock-wool-insulation/showroom/havelock-wool-insulation/lca-results
[17] Steel Recycling Institute (2022). Retrieved from Environmental Product Declaration – Steel Recycline Institute: https://cdn.scscertified.com/products/cert_pdfs/SCS-EPD-03838_SRI_CFS-Stud-Track_011916_web.pdf?r=1
[18] Isohemp Natural Building. (2022). Lifecycle Assessment: Isohemp Hempcrete Blocks. Retrieved from https://static1.squarespace.com/static/5ad125e089c172a00f0bd92e/t/5c6afb7c9140b77a89da213c/1550515071681/lca-isohemp-2018_0.pdf
[19] MOSO International. (2022). Retrieved from Environmental Product Declaration: MOSO Bamboo X-Treme: https://www.moso-bamboo.com/wp-content/uploads/20170315_EPD_INT_Moso_X-treme_EN.pdf
[20] National Ready Mixed Concrete Association. (2022). NRMCA MEMBER INDUSTRY-AVERAGE EPD FOR READY MIX CONCRETE. Retrieved from National Ready Mixed Concrete Association Environmental Product Declaration: https://www.nrmca.org/wp-content/uploads/2020/02/NRMCA_EPD10294.pdf
[21] Orr, G. A. (2020). A Brief Guide To Calculating Embodied Carbon. thestructuralengineer.org.
[22] Rockwool. (2022). Environmental Product Declaration: Rockwool Stone Wool Insulation. Retrieved from https://www.rockwool.com/siteassets/o2-rockwool/documentation/epd/rockwool-stone-wool-environmental-product-declaration-epd.pdf
[23] Rocky Mountain Institute. (2022). Retrieved from Reducing Embodied Carbon in Buildings: https://rmi.org/insight/reducing-embodied-carbon-in-buildings
[24] Spray Polyurethane Foam Alliance. (2022). ASTM Environmental Product Declaration: Spray Polyurethane Foam Insulation. Retrieved from https://pcr-epd.s3.us-east-2.amazonaws.com/450.EPD_for_SPFA_EPD_20181029_HFC.pdf
[25] The Brick Industry Association. (2022). Environmental Product Declaration; U.S.-Canada Industrywide Clay Brick. Retrieved from https://brick.com/sites/default/files/attach/bia_industry_wide_epd.pdf
[26] American Plywood Association. (2022). Glulam. Retrieved from https://www.apawood.org/glulam
[27] LEEDuser.buildinggreen.com. (2022). Environmental Product Declaration: EcoTouch PINK Fiberglas Batt & Roll Insulation – Unfaced and Faced. Retrieved from https://leeduser.buildinggreen.com/sites/default/files/credit_documentation/63_%20EPD_Owens%20Corning_EcoTouch-Pink-Fiberglas.pdf
[28] Pomponi, F., Saint, R., Arehart, J.H. et al. Decoupling density from tallness in analysing the life cycle greenhouse gas emissions of cities. npj Urban Sustain 1, 33 (2021). https://doi.org/10.1038/s42949-021-00034-w
TSW R&D Study: Embodied Carbon Content of Common Building Materials